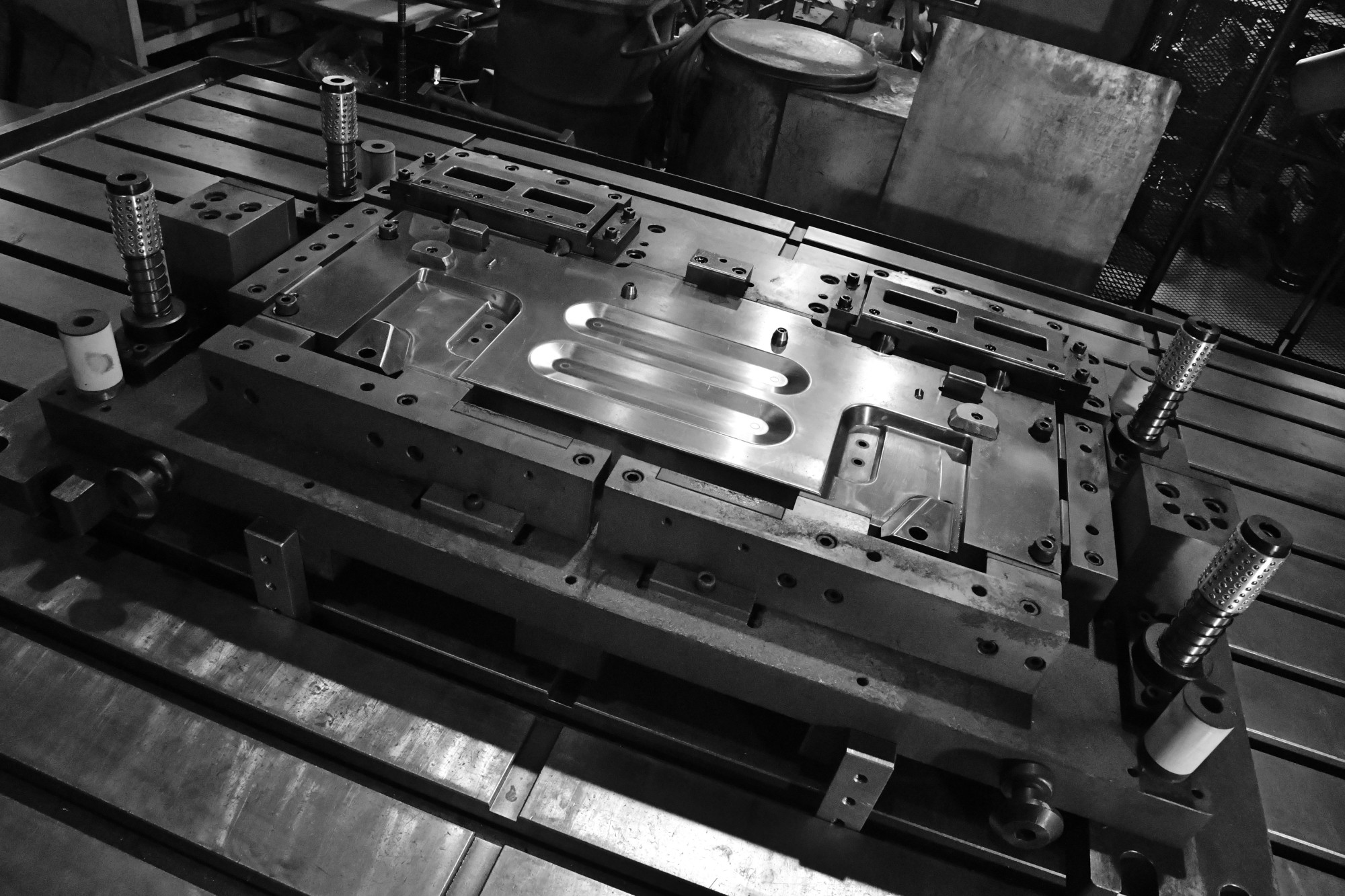
The world of automotive stamping is a rich landscape of metals and massive presses. A typical sheet metal stamp uses in excess of 2000 tons—the weight of 1000 typical sedans!
If you’ve never seen a sheet of metal go into a metal stamping press and come out as a car hood or firewall, you’re missing out. So what is automotive stamping? We’re going to bring shape to a whole industry of metal stamping, of which automotive stamping is just a slice.
Keep all hands and feet outside of the danger zone at all times, but keep your eyes on the article!
Automotive Stamping
Automotive stamping is an old industry, but metal stamping itself goes back at least as far as 1880 for bicycles. It didn’t take long for industries in the United States to form their own uses for the German innovation.
While metal forging produced stronger products, for most of the uses that metal stamped products serve stamping was good enough. This led entrepreneur, inventor, and industrial giant Henry Ford to finally give in and use the technology for mass production of his vehicles.
Why? Because while forging metal produces a “stronger” product, metal stamping is cost-effective and fast.
Just because it’s efficient and quick doesn’t mean it’s easy or simple to do.
Stamping vs Forging
In forging, you need several dies, which are not simple or easy to make. Forging is more like making bread, and the die is the bread pan. For comparison, stamping is more like making cookies and using a cookie cutter on a sheet of dough.
Three different types of dies used for forming the sheet metal are forming, cutting, or a die which does both.
As for cutting dies, they perform actions like:
- Notching
- Blanking
- Trimming
- Lancing
- Piercing
- Shearing
In stamping, you only need as many dies as you have stamping machines, but you can produce more than one part per press. It reduces turnaround with high accuracy products when you can make them by the dozen.
However, if you’re stamping the whole side of a car frame at one time, it’s going to be a large sheet. While stamping is a “cold” process, that is, no heat is introduced into the die or sheet, friction produces a lot of its own heat.
Depending on the size and complexity of the part, a job could entail 1,000 pieces or 80 million pieces, so it’s very flexible as well.
Stamped for Approval: Now You Know
Large or small? Complex or simple? Either way, metal stamping, and automotive stamping specifically, has been around for almost 150 years and is here to stay.
No doubt, as you look out the window, metal and automotive stamping have shaped our world. Not only is the industry process here to stay, but it’s also expected to grow over time. Get involved today and don’t miss out, you have our stamp of approval!
We’re in the business to supply you with more car facts than you’ll know what to do with! So, if you enjoyed this article as much as we did, keep reading!